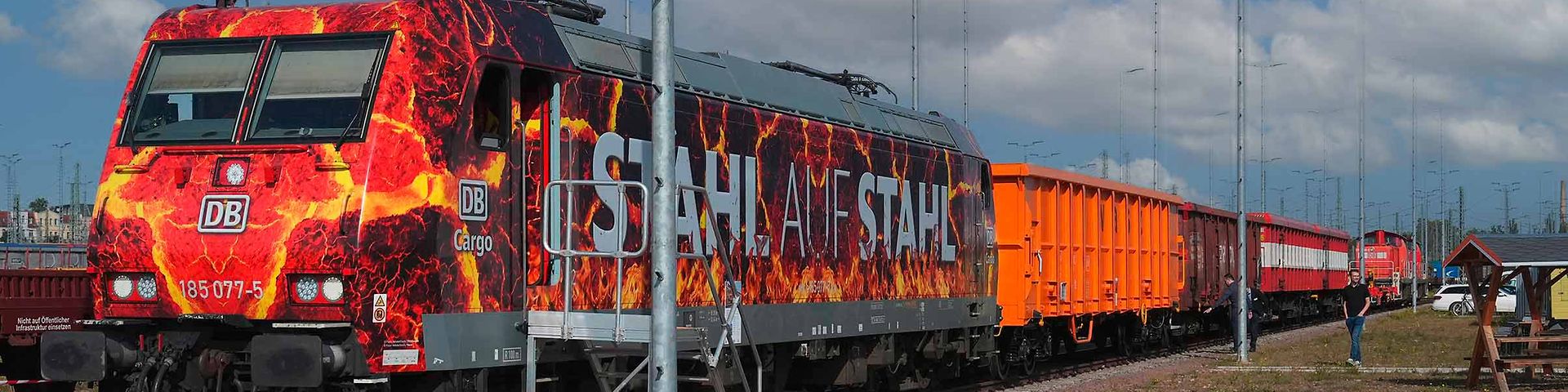
Moving raw materials together
DB Cargo uses modern equipment to support the circular economy in the steel and steel recycling industry.
Steel production in Germany is set to be carbon neutral by 2045. At present, however, producing one tonne of steel still releases 1.5 tonnes of CO2 into the atmosphere.
New technologies can help reduce these emissions. Germany's oxygen steelworks are therefore planning to gradually replace their coal-fired blast furnaces with direct reduction plants. These plants use hydrogen as an energy source, which reduces greenhouse gas emissions, although natural gas will be used as an intermediate fuel. This process creates sponge iron as an intermediate product, which is then refined together with scrap in an electric arc furnace to make raw steel.
Making this change reality will require Germany's large steelworks to be completely rebuilt: a long and expensive process. This transformation of the industry will see scrap steel become increasingly important. Scrap's sustainability credentials make it particularly valuable. Like no other product, it symbolises the idea of the circular economy. This is because scrap steel can be recycled as many times as needed without degrading from a metallurgical perspective. Scrap is therefore becoming a valuable raw material for green steel production.
Steel recycling, scrap or raw material?
Europe's largest rail freight operator has always been closely linked to both the steel industry and the steel recycling sector, and knows their needs inside out. Now, both industries are facing the biggest transformation in their history. DB Cargo is therefore working flat out with various partners to make transporting the valuable freight as simple and economically viable as possible. With this goal in mind, the company brought the various interest groups together at one table, or in this case one station, at the goods yard in Halle an der Saale in eastern Germany. The event was attended by the Federal Association of German Steel Recycling and Waste Disposal Companies (BDSV), as well as representatives from TransANT, Wascosa, Konecranes and Railroadbox. These all presented innovative solutions designed to enable or improve the transport of the raw material by rail.
One of the reasons for this is that not all scrap recyclers have their own siding. DB Cargo is now remedying this situation with new wagon and loading systems.
How is scrap steel transported?
Andreas Schwenter adds: "We should meet more often locally, or even hyperlocally. This will ensure everyone involved knows exactly what the needs are and what solutions already exist. Not just on paper, but real existing solutions." One of these is the Scrap Unit on DB Cargo's m2 wagon. Its modular design features a container attachment that gives both the consignor and the consignee maximum flexibility. The removable containers can be dropped off at the scrap recycling facility, before being filled and then loaded onto the train. Special forklifts like those from Konecranes can lift up to 65 tonnes and will soon be able to lift up to 28 tonnes fully electrically. They can do this even in the tightest of spaces and without a siding if necessary. This is because the standard containers can also be transported by HGV on the first or last mile. This is also true of the Railroadbox, a special container that can be tilted and is therefore suitable for other bulk materials too.
The classic Eanos wagons and the Wascosa flex freight system® continue to ensure reliable availability and loading efficiency for customers who ship large volumes via their own sidings.
"We are helping our customers make their logistics more efficient, increase the productivity of their freight wagons and reduce their rail logistics costs", continues Wagner, referring to the various wagon concepts. The TransANT wagons are also extremely efficient. They were developed specifically for voestalpine's transport operations, but could also be used for other customers in future.
Anja Pastl adds: "Our wagon is made from voestalpine's resistant lightweight steels, which makes it both very light and extremely resilient. These properties are important when it comes to loading scrap."
Get in touch with our expert.
Dima Koch
Senior Consultant Strategic Transport and Logistics Solutions, DB Cargo AG