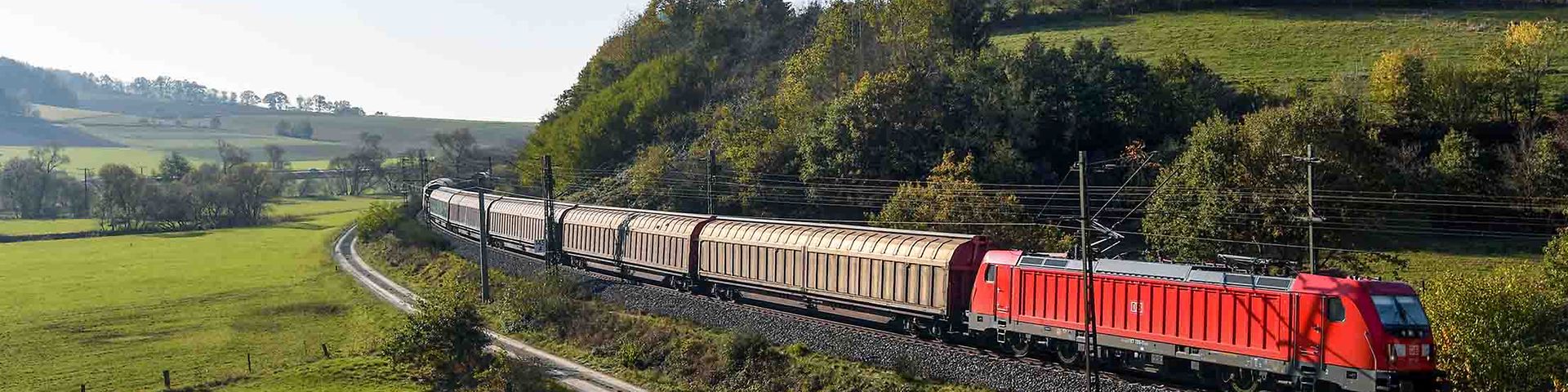
High-capacity battery transport by rail
DB Cargo Logistics transports cell modules to the Czech Republic for Volkswagen Group Logistics and the Škoda brand.
Electric vehicles are among the most important and visible factors in the transition to new drive technologies. But a true measurement of their carbon emissions should include not only the energy used to charge them but also the vehicles' production and transport – a view on which DB Cargo Logistics and Volkswagen Group Logistics agree.
Automotive RailNet: the perfect foundation
With its strategic vision of "zero impact logistics", Volkswagen aims to make its entire logistics chain as carbon neutral as possible. As a provider of battery transport services, DB Cargo Logistics is playing an important part in helping VW achieve that goal. Heavy goods such as batteries are well suited to rail transport.
Using DB Cargo's Automotive RailNet, DB Cargo Logistics has been transporting cell modules by rail from the port of Magdeburg to Mladá Boleslav in the Czech Republic since July. "With standardised and tested battery transport processes, we can respond flexibly to the needs of our customers," says Sören Labyk, account manager at DB Cargo Logistics. "Our plug-and-play approach plays an important role here by allowing us to add new transport services to the existing network quickly and easily."
Connecting with the existing battery network
From their manufacturer's warehouse in Magdeburg, the cell modules are brought to Magdeburg's port by lorry. Once they arrive at the port, the lithium-ion cell modules are protected from the elements while being transhipped, prepared for rail transport, and loaded into sliding-wall wagons. From there, the modules are taken directly to the Škoda plant in Mladá Boleslav, 370 kilometres away, where they are built into batteries for electric vehicles. These are either installed in the Škoda vehicles produced locally or transported by rail to the Volkswagen plant in Emden.
Three trips per day eliminate eight lorries
Up to three wagons per day are currently sent to the Czech Republic, and the volume could increase to more than ten wagons a day in the future. The figures are enough to avoid a significant volume of road haulage. A freight wagon can hold up to 64 tonnes – two and a half times more than a lorry. Specially designed battery racks allow the sliding-wall wagons to be used to their full capacity. Three freight wagons per day means eight fewer lorry trips, an important step towards a carbon-neutral cell module supply chain.
Environmental and safety considerations favour rail transport
Avoiding lorry trips is not the only reason to favour rail. A significantly higher level of safety also makes rail the ideal mode of transport for batteries and cell modules. Both these components are classified as dangerous goods that need to be transported in the most non-polluting way possible, and also quickly and safely. In terms of accident frequency, transport by rail is 42 times safer than by road. This mode therefore ensures safe, fast and low-emission shipments of one of the most important components for decarbonising transport.