Article: Always ready for action: DB Cargo's mobile maintenance team
Always on hand when it matters
Whether it's a defective brake, a blocked wheelset or an electronics problem - when a freight train breaks down, every minute counts. This is exactly when they are needed: DB Cargo's mobile maintenance teams. Equipped with special tools, digital diagnostic systems and lots of know-how, they ensure that locomotives and wagons are ready for use again as quickly as possible - and that traffic does not come to a standstill.
One team, many tasks
"We go out when technology needs support," is how one colleague from the team sums it up. As a rule, the day begins with a look at the production control system's resource planning - depending on requirements, the work is started from the site. The order is sent digitally to the tablet and the tools are packed appropriately. On site, the team analyzes damage, replaces defective parts and puts the vehicle back into operation immediately - all in compliance with the applicable regulations.
This not only saves time, but often also a costly delivery to the workshop.
From everyday life: Voices from the team
What makes the work special? The mixture of technology, team spirit and flexibility. One maintenance technician describes: "Every assignment is different. Whether in the middle of the night or in heavy rain - we have to react quickly and work with the utmost care at the same time." Challenging, but that's what makes it so appealing.
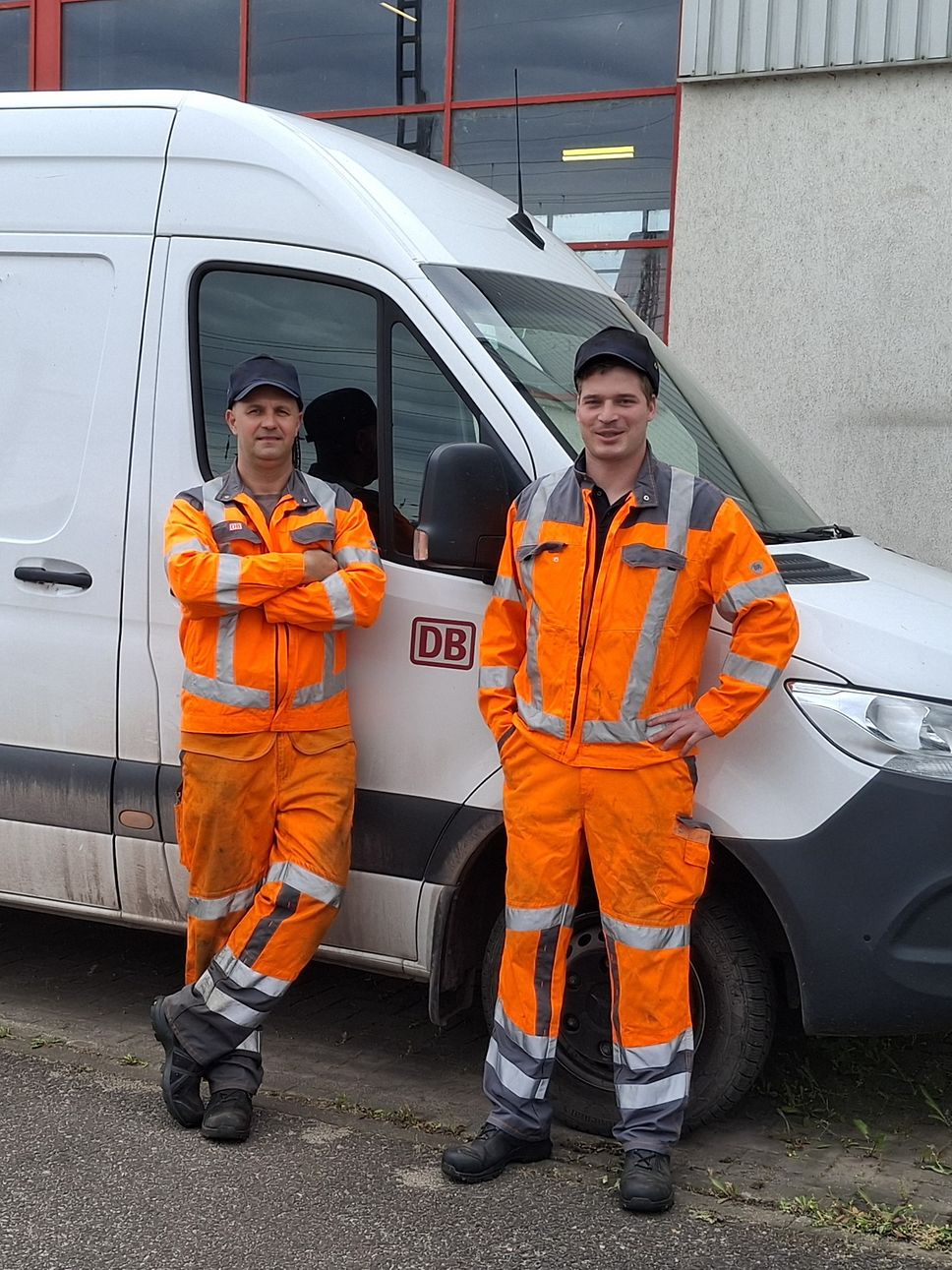
Jörg F. and Patrick R. - part of the Magdeburg plant team - in front of the emergency vehicle in the field.
The qualifications are also diverse. We employ mechatronics engineers, locomotive fitters, industrial mechanics and electricians - all with specific rail training and additional training courses, for example for certain series such as the BR 185 or BR 261.
Technology on board
The service vehicle contains service computers with special software, diagnostic tools and mobile work equipment. Programs such as dmCube (control system navigator), KRWD (technical documentation) or DB MatID (material identification) support the work - as do tablets for order management.
Spare parts are packed individually depending on the damage report - and often a single visit is enough to solve the problem.Commitment with responsibility
Troubleshooting and repairs on site - that also means responsibility. "We can't make any mistakes, there's too much at stake," says a colleague. That's why we check whether the team can provide any meaningful help at all before they are deployed - in other cases, emergency technology takes over. Improvisation? Only in the head. If a part is missing, it is not tinkered with, but professionally readjusted - in the interests of safety.
A career with prospects
Many of the colleagues completed their training at DB Cargo. One team member explains:
"I started out as an industrial mechanic in wagon maintenance and then specialized in locomotives. Today, I'm a train driver and support the mobile team when needed." The development opportunities are varied: from foreman to production controller to maintenance officer, there are many paths open to dedicated specialists.What makes the team special
It's not just the know-how, but the team spirit that counts. "Everyone helps out, everyone is reliable," says one employee. Trust and team spirit are particularly important when working outside of regular hours - and you can feel this at every level here.
This article was produced with the kind support of the Magdeburg works team. Special thanks go to Anton Graf (Deputy Foreman) for the insights into everyday operations - and to his superior, Mr. Peter Kein, Head of Production Locomotive/Wagon Branch Magdeburg, for making the exchange possible.