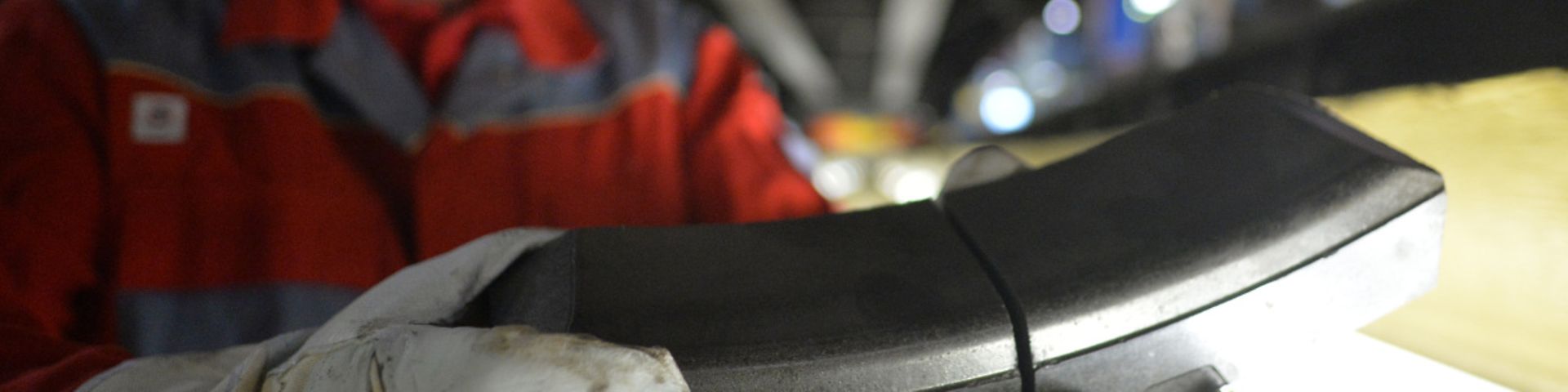
Noise control: Whisper brakes remain the best solution
At the beginning of March, the trade press reported on an alleged "lack of functionality of composite brake blocks under Scandinavian winter conditions."
At the beginning of March, the trade press reported on an alleged "lack of functionality of composite brake blocks under Scandinavian winter conditions." There has been speculation that isolated reports of problems said to have occurred in northern Sweden during certain unusual winter weather conditions could lead to the end of the composite brake block (whisper brakes) throughout Europe.
Here are the facts and a brief explanation of DB Cargo’s view of the discussion.
Rail freight transport is the most environmentally friendly means of transport. But for rail to grow, it must reduce the noise emissions it causes. In Germany, for example, more than 200 freight trains already run daily in the Rhine Valley, more than 100 of them at night, resulting in numerous noise complaints from residents. Residents not only complain about the noise, but blame loud freight trains for a range of health problems. The need to reduce noise is also highlighted in the 2018 European Railway Agency (ERA) Impact Assessment and, in early 2019, led to the amendment of TSI Noise, which regulates the technical specifications for the interoperability of wagons with regard to noise emissions.
The use of composite brake blocks can reduce rail noise emissions by preventing wheels from roughening and thus eliminating the main cause of rail noise. Using composite brake blocks thus reduces noise emissions at the source, allowing smooth wheels to run on smooth rails, and results in a 50% reduction in perceived noise. Since 2007, all new wagons in Europe have been equipped with type K composite brake blocks and older wagons have primarily been outfitted with type LL composite brake blocks since their approval in 2013. The established cast iron blocks can be replaced with a type LL composite brake block without any major changes. Unlike with the type K brake block, the brake system does not have to be modified to accommodate the new brake block. For this reason, type LL brake blocks are usually chosen to convert older freight wagons. The cost for the conversion to type LL blocks is roughly EUR 1,700 for each four-axle vehicle, which is around two-thirds less than for the type K brake block. The conversion of fleets in Europe (a total of around 400,000 freight wagons) to type LL blocks thus represents an economically feasible option to significantly reduce rail noise emissions.
DB Cargo now has around 59,000 quiet freight wagons with composite brake blocks. These wagons have now covered about 4.9 billion wagon kilometres in Europe, roughly ten times the distance to Mars and back. During this period, no countries aside from Sweden and Finland (which reported problems) had any issues of the type reported in Sweden while complying with the UIC application guidelines for composite brake blocks.
Conclusion: The composite brake blocks are winter-proof and provide an effective and economically feasible way to reduce noise emissions for 99.5 percent of European traffic in a highly competitive transport market. Sweden's transports to and from other European countries account for some 0.5 percent of all European traffic. A solution must therefore be found which is feasible for Sweden, which ensures Sweden's traffic with other European countries is not jeopardised, and which, at the same time, does not call into question the use of composite brake blocks, which are an affordable and winter-proof option for other European countries.
The use of disc brakes, the alternative proposed by Sweden and mentioned in discussions in the media, is not a viable solution for Europe considering the huge number of older freight wagons currently in use. Disc brakes also use composite brake pads, and there is no empirical evidence that they are more suitable for winter conditions. Since it costs between EUR 20,000-30,000 to convert a wagon to a disc brake system (totalling some EUR 10 - 12 billion for converting the entire European fleet), this does not represent a viable option and would jeopardise freight rail transport in large areas of Europe in which it is subject to severe intermodal competition. The 0.5 percent of traffic that involves Sweden may not be allowed to jeopardise the 99.5 percent of traffic that takes place in the rest of Europe.
Rather, it is necessary to examine the different layers of the problem, concentrate on the actual core issue and find suitable solutions. There are no problems with winter conditions in northern Sweden during the summer, and even in winter, southern Sweden rarely experiences any such issues. And even in northern Sweden, the problems reported in winter only occur under certain unusual weather conditions. Considering this, we must develop operational rules for this special situation, such as driving with reduced speeds, periodically braking to free up the braking system, or forming trains in such a way as to ensure that they include wagons with composite brake blocks and, in Sweden, wagons with cast iron blocks. As a comparison, keep in mind that if there is black ice on motorways, road vehicles have to drive more slowly or even stop. No one would suggest that trucks throughout Europe should be outfitted with studded tyres so that they can continue to drive 80 kilometres an hour on black ice.
We are certain that by working together in the rail freight sector, we will find solutions for the problems that occur under Swedish winter weather conditions. These solutions must meet safety requirements and ensure that the Swedish network remains technically integrated with the rest of Europe without jeopardising the viability of rail freight transport throughout Europe by requiring excessive investment in brake system conversions.
More about noise control