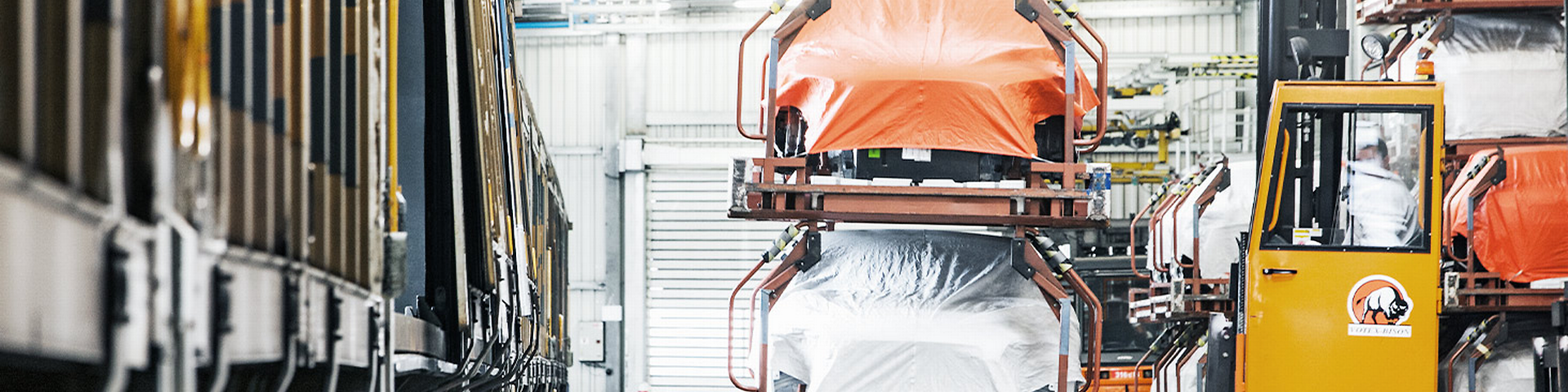
A new era for DB
Deutsche Bahn and the Volkswagen Group have a long tradition – now the car manufacturer and DB Cargo are gearing up for the future.
DB has become one of the most important service providers for the carmaker over the decades. The logistics company brings the full scope of its expertise and a vast network to today's complex supply chains to enable environmentally friendly transport between manufacturers, suppliers and customers.
One of the products of Germany's economic miracle was greater mobility. Germans wanted to travel more, and farther afield. And cars weren't the only mode of transport to gain in popularity in the early post-war years. Rail also grew to become one of the most important service providers for the Volkswagen Group in Wolfsburg. Volkswagen established Wolfsburger Transport-Gesellschaft mbH, now Volkswagen Konzernlogistik GmbH & Co. OHG, in 1965 to coordinate and develop its own transport activities in its growing production network.
Today, Volkswagen is Europe’s largest automaker. "We offer Volkswagen a range of services that span the entire value chain – including finely tuned just-in-sequence delivery to assembly lines, car transport to seaports and European distribution terminals, and industrial railway operations," sums up Jens Nöldner, CEO of DB Cargo Logistics. DB Cargo is continuously expanding its existing solutions to be able to transport even more freight and meet the many different requirements of this remarkable company.
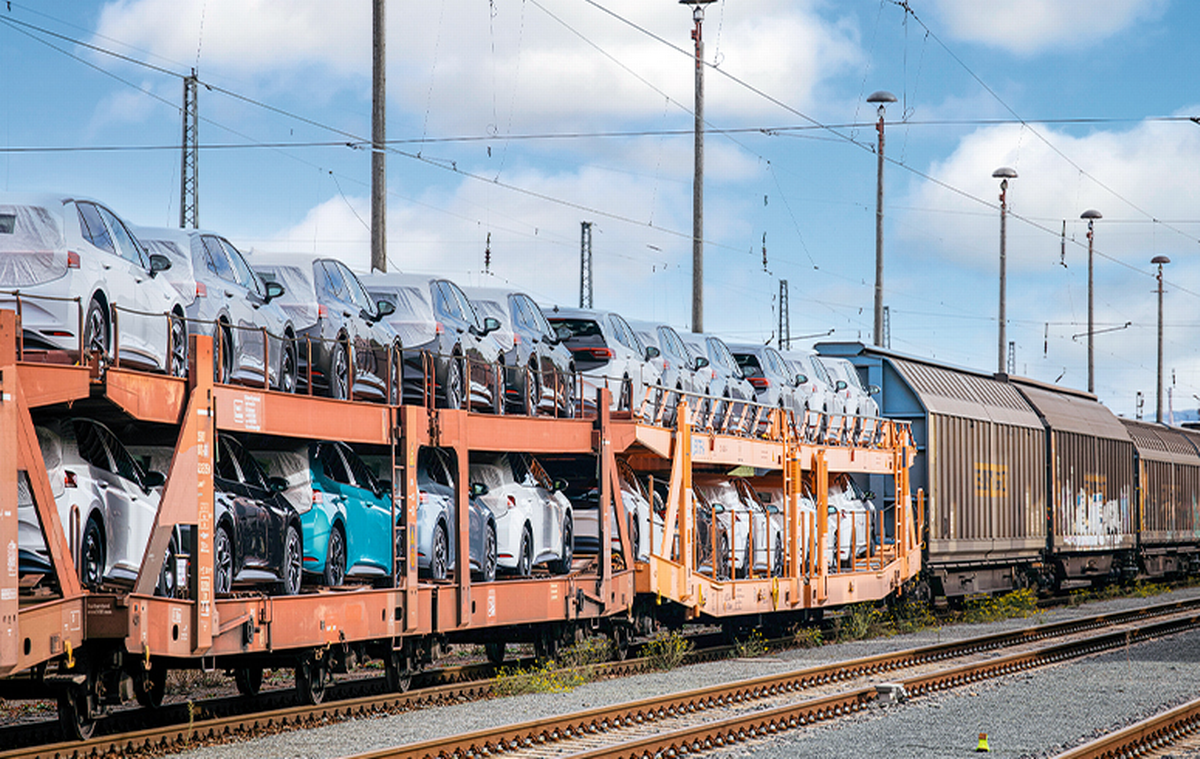
DB Cargo Logistics hasan equipment f leet for various customer requirements. Its car carrying wagons are equipped with two loading decks for transport throughout Europe. Copyright: Oliver Killig
A vast network throughout Europe
The network that DB Cargo Logistics has created for Volkswagen stretches from Spain and Portugal to Poland, from Norway to Italy and eastward, all the way to the company's production sites in Kaluga and Nizhny Novgorod, Russia. Cross-border block train and single wagonload service, multi-system locomotives and smart freight wagons connect 18 warehouses for OEM parts and up to 20 plants that produce the Volkswagen Group's brands. Volkswagen's components business forwards some 160,000 consignments every year by rail. DB Cargo Logistics provided around 8,500 trains for these shipments in 2019.Volkswagen's new vehicles also make their way by train to customers in Europe and overseas. DB Cargo Logistics transported 800,000 new cars in 2019 on its rail network, which connects 14 plants to 30 ports and access points via various hubs.
Component transport beyond borders
The enormous complexity of logistics tasks becomes apparent especially when components are transported internationally. Volkswagen needs automotive parts in many different stages of completion to be delivered to its assembly lines. On average, every vehicle consists of around 4,000 individual components, which are assembled in one place. Since components come from suppliers around the world, supply chains need to be lean and stable and work without hiccups for years on end. This is why the VW Group's brands lay out in detail which vehicles are to be produced and when. Every component plant and every supplier is informed exactly when parts need to be made available for production. Then it's up to DB Cargo Logistics. Employees at the Components unit in Hanover make sure that trains transporting components depart on time with the required volumes.They need to cross national borders, too. DB Cargo Logistics has transported vehicle components from Germany and the Czech Republic to Kaluga and Nizhny Novgorod, Russia, and coordinated a number of operators and subcontractors since 2007. Trains make the journey from Wolfsburg to Kaluga in five days. The logistics specialists are especially proud of their smart IT solutions, which have streamlined customs and border processes at the border between the EU and CIS in Brest. The service has been a resounding success. DB Cargo Logistics transported its 500,000th container from Germany to Russia in 2020. Lined up end to end, the containers would stretch from Berlin to Moscow roughly four times over.
Rolling stock designed for the automotive industry
While some routes have remained the same over the years, the technology and methods used have made tremendous strides. "Ten years ago, we were only able to transport from one private siding to another. For anything more complex than that, customers needed to have their own expertise," says Kai Birnstein, who heads the Components unit at DB Cargo Logistics. "We now have an extensive network of partners for vehicle transport, access points for transhipping between road and rail, and so much expertise that we're able to offer efficient integrated concepts."These developments allow DB Cargo Logistics to draw up bespoke solutions for the automotive industry. Take rolling stock, for example. In the early days, traditional stanchion and flat wagons were used to transport cars to distribution centres and customers. DB's predecessor began designing special car transporters back in 1953. The best known is probably the double-decker Off 52, which is even available in miniature from model train maker Märklin. DB Cargo Logistics now has a wide range of wagons that the Group and some of its close partners developed specifically for transporting certain types of vehicles: wagons with a top loading deck whose height can be adjusted to accommodate SUVs and vans; flat wagons for especially large commercial vehicles; and TT wagons for transporting components, with a headroom of three metres, providing roughly as much space as a lorry.
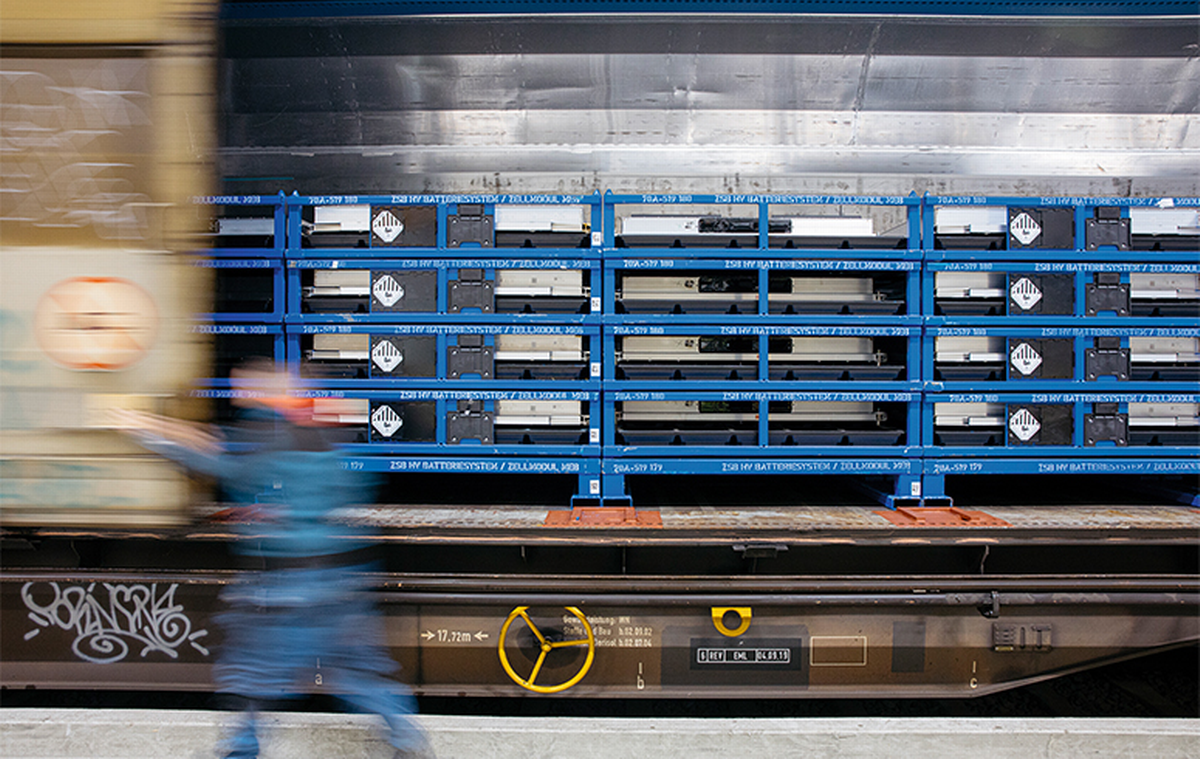
The high voltage battery has a modular design and contains up to 12 battery modules, each with 24 lithium ion cells. Copyright: Oliver Killig
New logistics concepts for changing markets
Through decades of experience, DB has managed to quickly and reliably identify the needs of the automobile manufacturer in lockstep with modernity. "The market's logistics requirements are changing, and we're developing new solutions with our customers. Our network puts us in a really good position to increase rail's share of vehicle distribution in the future," says Alexander Röckelein from the Finished Vehicles team at DB Cargo Logistics. It's no easy task, because Volkswagen is constantly reinventing itself.Logistics is constantly evolving, too. A driver shortage, stricter rules for drivers and traffic in Germany have made trucks much less flexible than they were a few years ago, for example. As a result, transport solutions that combine multiple modes are now increasingly important. DB Cargo relies on its partners or DB Schenker for all-in-one international multimodal solutions. "Many of our services benefit from solutions that we developed with the DB Cargo companies and other DB Group companies," says CEO Jens Nöldner. "Cooperation within the Group allows us to offer our customers services that are the perfect response to carmakers' needs."
Sustainability, e-mobility and digitalisation: topics for the future
Sustainability is another trend that is turning the market inside out. "Carbon emissions have become one of the most important issues in the automotive industry," says Birnstein. The modal shift is necessary from a climate policy perspective. Transport is much more sustainable when the long main legs are covered by rail, and lorries handle only the first and last mile.The conversion to electric mobility will bring about a fundamental structural change, not so much on the logistics side, but in terms of the range and design of supply chains. This includes transports for lithium-ion cells: DB Cargo Logistics provides sustainable transport for battery and cell modules, and parts for the new fully electric Audi e-tron. Deutsche Bahn has partnered with Volkswagen Konzernlogistik to set up a sustainable logistics concept.
Going forward, the plethora of railports, terminals, hubs, logistics centres and other track access points that DB Cargo Logistics and its partners are building and operating all over the map will help us to handle even more transports by rail and to shift cargo, too. Along the main routes in Germany, however, capacity utilisation is already strong. Here, digitalisation will help increase infrastructure capacity. Comprehensive digital control will make it possible to up traffic in the network by nearly one-third. Carmakers are already using digital advancements, such as artificial intelligence and the internet of things (IoT). The Volkswagen Group connects its 125 plants around the world via a cloud so that it can identify delivery bottlenecks and incidents early on.
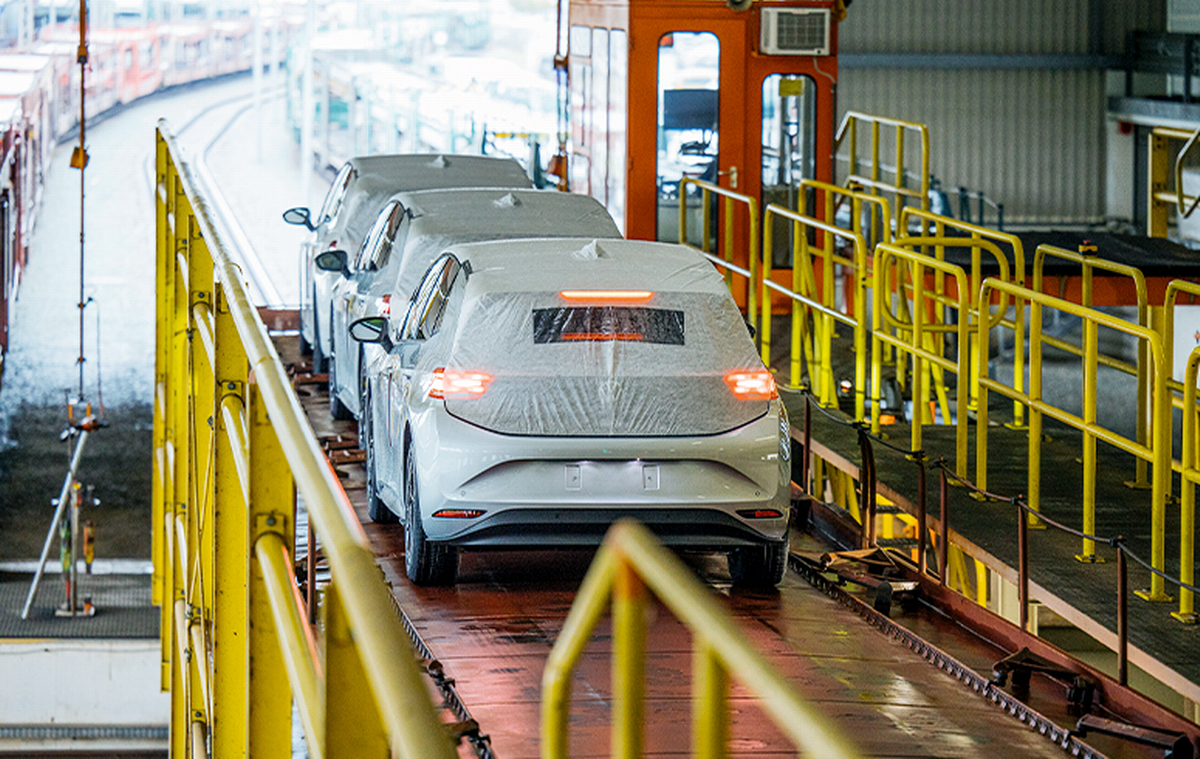
The Zwickau vehicle plant produces vehicles including the fully electric ID. Copyright: Oliver Killig
Rethinking logistics chains
With the assets of sustainability and digitalisation, DB Cargo intends to keep developing its portfolio of products while expanding its services for the Volkswagen Group. Its prospects are looking good. One thing that's not going to change is its large, European network, which is one of the key advantages that allows it to quickly respond to customer's changing parameters. This highly efficient infrastructure, combined with the decades of experience of its employees and state-of-the-art technology, is what will create logistics solutions that will be essential to automobile production and distribution in the future. "We will be able to achieve what we have planned for Volkswagen in the coming years only as part of a close partnership with the company. We need to rethink logistics chains," says Kai Birnstein. "It's the start of a new era for us."