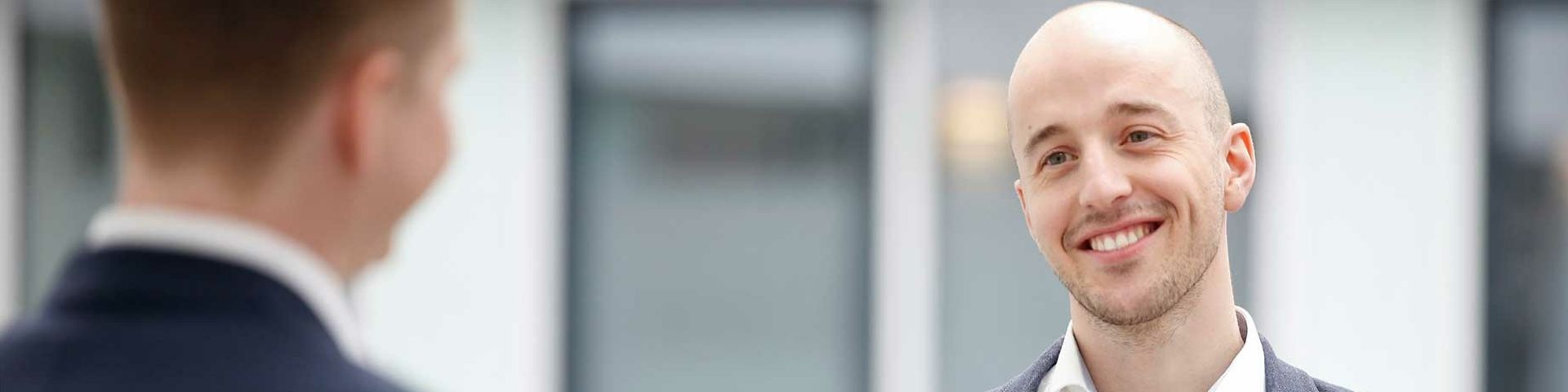
CATL launches green battery logistics
The leading manufacturer of lithium-ion cells for electric vehicles teams up with DB Cargo to transport battery modules by rail.
Chinese company CATL (Contemporary Amperex Technology Co. Limited) is the world's largest manufacturer of batteries for electric vehicles. Since January 2022, DB Cargo Logistics has been handling multimodal transport of lithium-ion cell modules in steel frames for CATL. The goal is to transport the battery modules mainly by rail, making the entire supply chain for electric cars more sustainable. We spoke to Robert Richter and Patrick Möhle, automotive account managers at DB Cargo Logistics.
How and when did you first make contact with CATL?
Robert Richter_ We have maintained regular contact with CATL for quite some time. The planning for this specific concept started in spring of 2021. Since then, we have been working ever more closely together and have now implemented the concept.What exactly does the concept look like?
Patrick Möhle_ Our transport concept is to collect finished batteries from the CATL warehouse in Erfurt and drive them by lorry to Eisenach. One of our service providers loads the batteries onto freight wagons there. We then move the batteries by rail through our existing Automotive RailNet from Eisenach to the car manufacturer.What was the initial situation when CATL approached you?
RR_ Our customer, a well-known car manufacturer, was looking for rail delivery of the batteries for its electric vehicles. One challenge was the fact that CATL, the battery supplier, did not have a private siding at its site in Erfurt where the cell modules are temporarily stored. We therefore set out to find suitable logistics infrastructure in the region to transfer cargo from road to rail. We finally found a suitable transhipment facility in Eisenach.What steps did you identify and how did you implement them?
PM_ We prepared and set up the logistics concept while always coordinating with the supplier CATL and with the end recipient, the car manufacturer. Throughout the process, we continuously adapted the concept to fit the new requirements until the launch was approved by all parties involved.RR_ Ultimately it was a parallel approach: we planned the concept with our customer while also considering the requirements of the service providers involved.
What kind of site in Erfurt do the battery modules come from?
RR_ CATL is building its own factory in Arnstadt now to be able to produce cell modules in Germany going forward. In the meantime, CATL is importing the modules from China. CATL currently maintains a warehouse in Erfurt to temporarily store the cell modules, where they are given another thorough check. Only then does our subcontractor drive the modules to Eisenach on trailers specifically acquired for the job. Once they arrive, they are reassembled and loaded for transport by rail.What USPs can DB Cargo Logistics score points with when it comes to battery logistics?
PM_ The fact that we offer complete solutions is definitely a unique selling point. We provide our customers with bespoke, door-to-door solutions – which we control from a single point. The advantage for the customer here is that there is no need to work with several service providers and coordinate between them. By managing everything in one place, we can implement the relevant logistics concepts holistically and cater to the rising demand for environmentally friendly rail concepts. It helps that we have internalised the rail logistics philosophy of shifting as much cargo to rail as possible. To do this, we coordinate closely with our suppliers – to set up underlying processes for logistics handling, for example. This means that we don't just run trains from point A to point B but take a holistic view. What sets us apart at DB Cargo Logistics is the fact that a dedicated project team guides the concept all the way from initial discussions to implementation. This makes us much more approachable to our customers.How important are sustainability and safety in battery logistics by rail?
RR_ Very important. That said, lorries will continue to play an important role in fully linking the various modes of transport, not least because not all suppliers have a rail siding. We can leverage the flexibility of lorries here, and perhaps even electric trucks in the future. However, owing to rail's ability to handle bulky cargo, rail-based battery logistics is faster and more efficient for heavy cell modules in particular. It's more environmentally friendly, too, of course. What's more, rail is 42 times safer than road – in terms of accident frequency. That's no small matter when you're transporting lithium-ion cell modules, which are class 9 dangerous goods.What makes this transport so appealing for your customer?
PM_ An important point is that the car manufacturer needs daily transports. That means that we pick up wagons daily and deliver them daily, too. This is only possible because we have the ability to reload the relevant cargo every day. We started in mid-January 2022 with one wagon per day, and we have now made it up to three wagons per day so we are ramping up nicely. Our concept is also designed to accommodate this growth in volume. It is scalable yet flexible enough for us to respond to the shifting requirements of the car manufacturer at any given moment.RR_ In a rail wagon, for example, we have space for more than 60 tonnes of useful load. This really brings out the big advantage we have over lorries, whose payload tops out at 24 tonnes. We can replace around two and a half lorries with one wagon.
PM_ In addition, we don't have to run the wagons in block trains. Instead, we can process them with our single wagon network, enabling us to bring this cargo to the automobile plant with appealing run times. As soon as the cargo volume rises again, we will be able to talk about block trains between the specific sites, too. It is precisely the flexibility of the single wagon network that is our big advantage at DB Cargo. It gives us the edge in battery logistics, even with smaller volumes.
Green battery logistics is currently seeing enormous demand. Is this view correct?
RR_ Yes, this is a very fast-moving area at the moment. Thanks to our customer focus, we can handle this dynamic change with our plug-and-play approach, which we use to connect new battery manufacturers to our network throughout Europe. Just like a USB stick, it's relatively quick and simple for us to link new providers such as CATL into our complex Automotive RailNet through logistics centres, railports and terminals. This way, the network is gradually developing into its own battery network, which we can use to efficiently connect suppliers and car manufacturers and the production facilities behind them.Lastly, a look into the future: What trends do you see in battery logistics and how can DB Cargo Logistics support new and existing customers?
RR_ I can only speak for us: First and foremost, we want to offer the greenest possible logistics chains – from a single source and conceived with a holistic approach from start to finish. This also includes multimodal logistics chains. In other words, also using lorries as a mode of transport, where necessary.PM_ Our aim is to further expand our Europe-wide Automotive RailNet so that it also becomes a network for transporting batteries. The basis for this is our strong expertise when it comes to handling, storing, sequencing and delivering battery modules. We have implemented all of this successfully in the logistics concept for CATL.