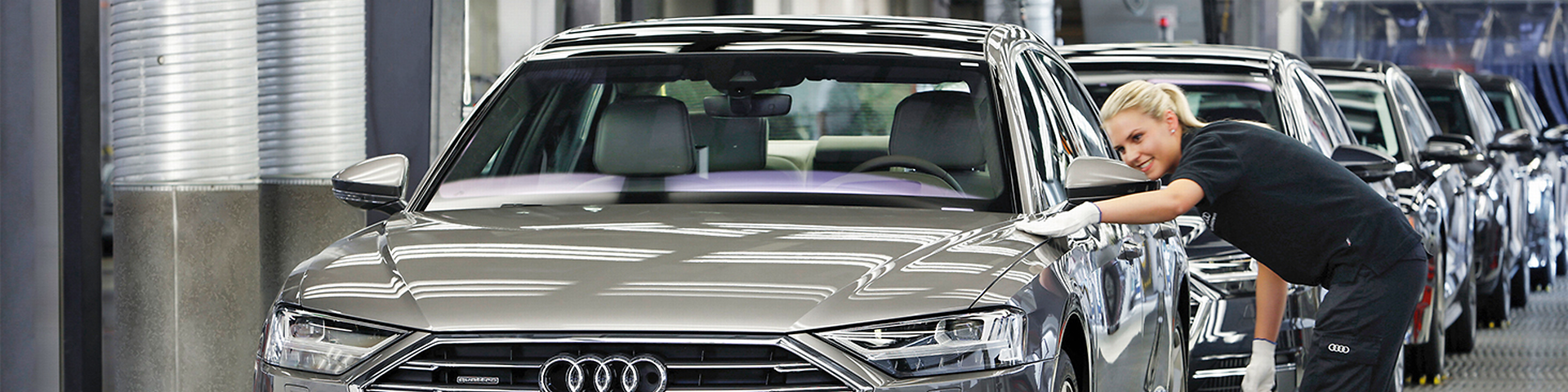
Supplier traffic moves to rail
DB Cargo Logistics: use multimodal transport to link Magna to Audi’s network.
Until now, suppliers of big-name car manufacturers have struggled to create multimodal supply chains. Having recently won the contract to transport purchased parts for Audi, DB Cargo Logistics has successfully seized the opportunities to be had from combining different modes of transport. The new solution, which replaces exclusively road-based transport between Salzgitter and Neckarsulm, has enhanced the customer's profitability and sustainability.
Customer-focused concept
Since October 2019, DB Cargo Logistics has been transporting products from automotive supplier Magna Stanztechnik in Salzgitter to Audi's plant in Neckarsulm. Subframes are manufactured in Salzgitter and installed in Neckarsulm. "Our customer-focused approach has succeeded in connecting a supplier with no active private siding to the existing automotive network," explains Heike Armgart-Tilch, account manager at DB Cargo Logistics. "Deutsche Bahn's subsidiaries handle all transport logistics from A to Z, so this is a genuine DB product."Lead logistics provider
"It's a very appealing solution for us," says Aranka Schiekel from Audi's inbound transport planning department in Neckarsulm. "It provides us with a central point of contact for managing the entire supply chain: organising and handling collection, transhipping cargo in Braunschweig, transporting the goods to Neckarsulm and returning the empties." As lead logistics provider, DB Cargo Logistics manages multimodal transports in collaboration with DB Schenker in Braunschweig. Operations are handled by the DB Cargo Logistics dispatching tower in Kelsterbach. If required and when cargo volumes increase, lorries make special trips in tandem with regular rail services to keep the plant well stocked.Strategic partner DB Schenker brings the freight by road from the Magna plant to a transhipment facility some 20 kilometres away in Braunschweig, which is connected to the automotive rail network. From there, it is forklifted onto DB's own freight wagons and prepared for onward transport to Neckarsulm. "We were able to enlist our high-capacity automotive wagons and traditional transhipment methods to make this model economically appealing. We can cleverly combine modes of transport to fit over 10% more cargo volume into every shipment we move," says Armgart-Tilch. Given the positive experience from this pilot project and the solution's scalability, DB Cargo and Audi are now working to provide similar transports elsewhere and to roll out the approach at other locations in Europe.
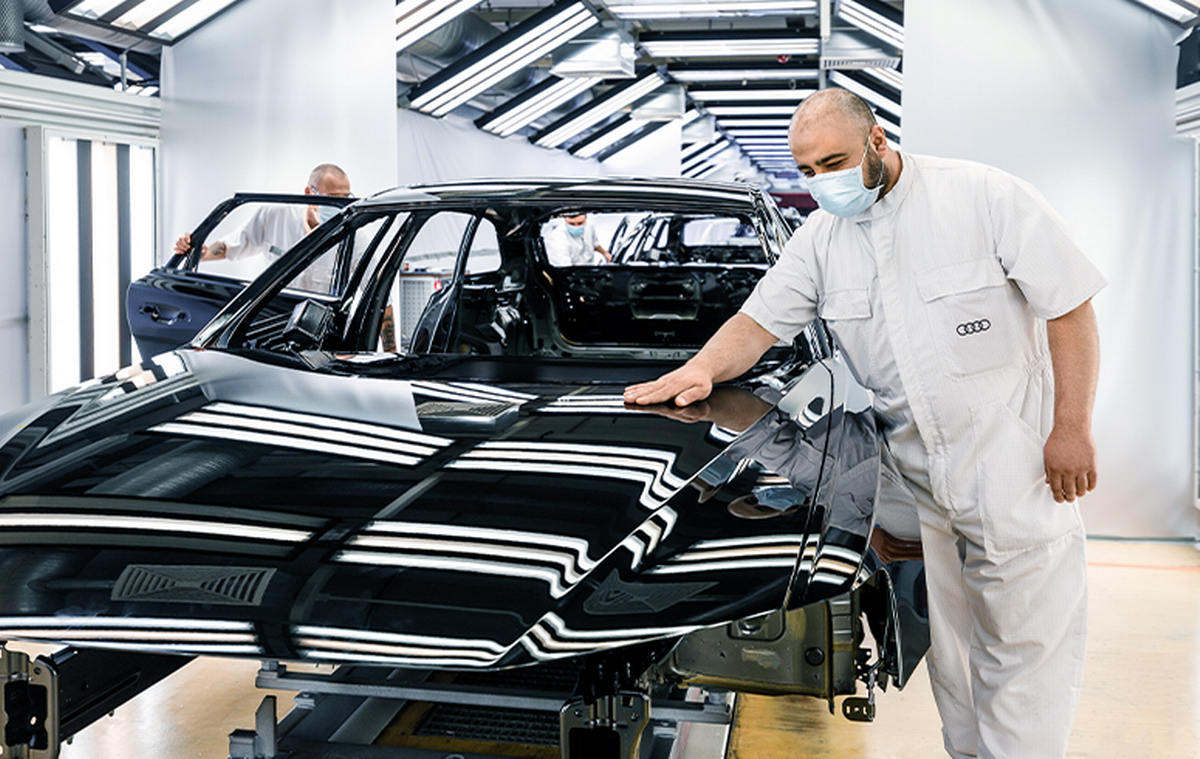
The nearly 17,000 employees in Neckarsulm manufacture around 180,000 vehicles a year (2019 figure) – including the A8. Copyright: Audi
Intensive preparations
The two DB subsidiaries underwent an intensive preparatory phase and carried out a test transport before they started working together. "The project had an almost perfect start, and communication between the individual interfaces worked from the very beginning," says Uwe Sanojca, head of DB Schenker's Braunschweig operations centre. "We have the ability to react promptly to any changes in the transport process, whether they stem from the supplier (Magna, in Salzgitter) or the recipient (Audi, in Neckarsulm)." From Braunschweig, an average of four covered freight wagons a day travel to the Audi plant, which has its own private siding. The Audi services offer DB Cargo two direct advantages. Firstly, supplier transports are better integrated into sustainable transport chains. And secondly, network utilisation and stability are increased. "This traffic goes to show the appeal of road-rail cooperation for customers when both modes of transport can leverage their advantages: flexible first and last mile by lorry combined with a main, environmentally friendly leg by rail," says Uwe Sanojca of DB Schenker.“This new concept lets us put our own infrastructure to optimal use.”Gerald Wohlfarth, Supply Chain Inbound Transport Planning, Audi AG
Optimum rail infrastructureDBeco plus makes rail transport CO2-free.
Audi is reaping the benefits of the new concept. "We have been able to better utilise our own infrastructure while mitigating the existing weaknesses of traditional CT handling processes," says Gerald Wohlfarth from Audi's inbound transport planning team in Neckarsulm. There is also the sustainability aspect: "We have been able to continue optimising our rail infrastructure, thus contributing to meeting our company's business and sustainability targets," he adds.