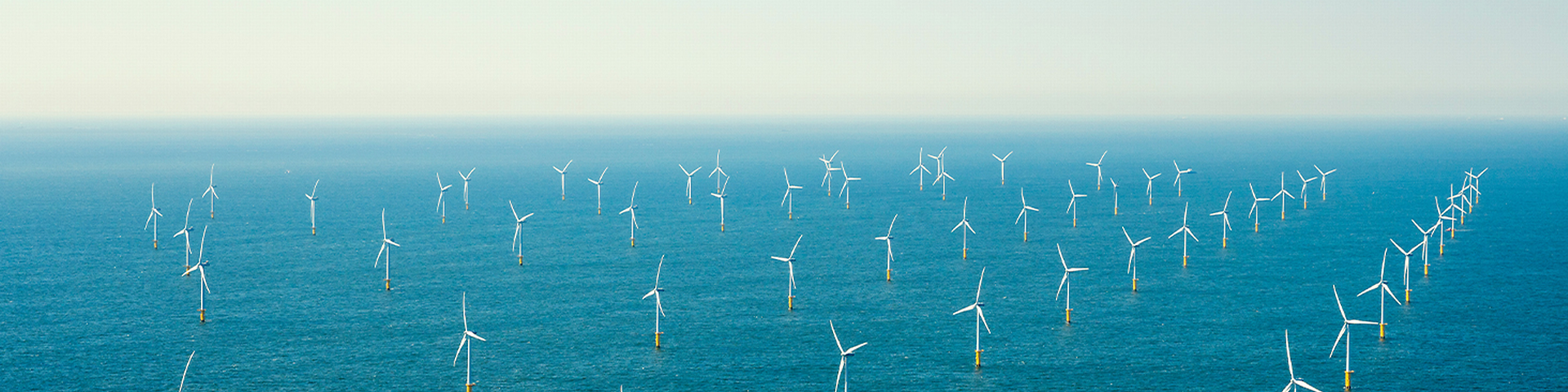
Towards sustainable steel
Together with Saarstahl and Dillinger, DB Cargo shows what sustainable logistics concepts look like.
When it comes to sustainability, the steel industry is not exactly in the front of the pack. But even for steel, environmental friendliness is gaining ground. DB Cargo, Saarstahl and Dillinger design sustainable logistics solutions together, helping Saarland's steel sector to cut CO₂ emissions. An overview.
Steel production requires a huge amount of energy, so the sector is constantly working to obtain this power from sustainable sources. Some innovative ideas include new supply models, the use of hydrogen and the development of efficient processes with low energy needs. Sustainable logistics is another approach. SHS StahlHolding-Saar (SHS), the parent company of Dillinger and Saarstahl, has four production sites in Saarland. The company considers sustainability to be particularly important, and it has found a dynamic partner for this priority in DB Cargo.
"We are SHS's partner for efficient and eco-friendly logistics concepts," says Katja Sander, head of sales at DB Cargo's Metals 1 team. "Whether it's incoming raw materials, inter-plant shipments or steel transportation services, we handle transports with a combined volume of some 10 million tonnes every year," says Sander. Ever-closer cooperation between SHS and DB Cargo in recent years has prompted the steelmaker's strategic choice of the DB subsidiary as its service provider. The steel manufactured by Saarstahl and Dillinger in Saarland is used for many purposes – making wire for the car sector and sheet metal for offshore wind turbines are just two of them. DB Cargo and SHS have worked together to come up with innovative concepts for supplying plants and transporting finished products.
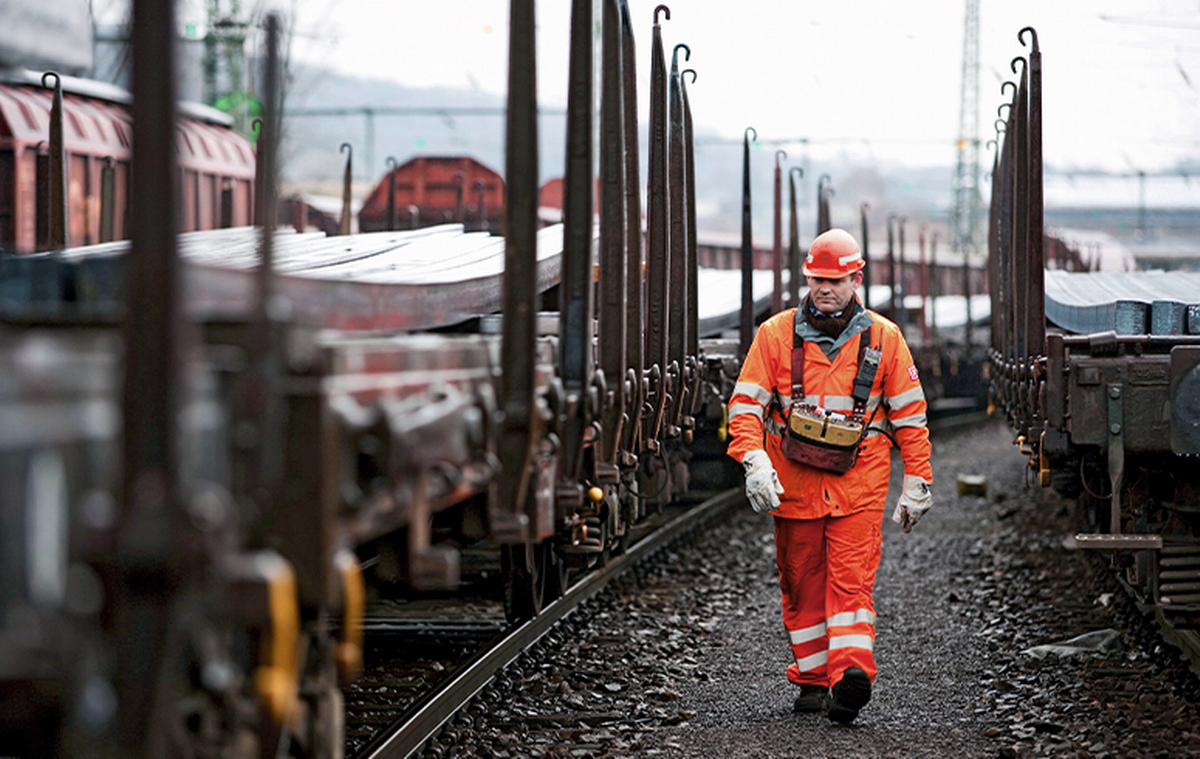
Steel wire and rods are normally transported in Rilsy, Rsy or Res wagons. Copyright: Michael Neuhaus
Shuttle system with short transit times
One of their solutions is the shuttle system, which combines short transit times and the flexibility of the single wagonload system. First, SHS's freight is consolidated and then transported by shuttle train to various destinations, such as the Ruhr district. Then, consignments are rerouted to their final destinations via high-performance marshalling yards. "Combining freight like this means we can make maximum use of train capacity," says Stephan Denzer, key account manager for Saarstahl at DB Cargo. "This gives the railway a further environmental edge over road transport, even as we use fast overnight services to move our cargo," he adds. Efficiency is also a priority in inter-plant transport. SHS and DB Cargo have developed an optimised concept which enables them to use a single train to supply several plants at once. Michael Grossmann, head of global logistics at SHS, says, "This not only increases efficiency but flexibility too, which is an important consideration, particularly given the reality of ever-shorter delivery cycles."Transfer to trains
The companies' cooperation has already resulted in a measurable drop in CO₂ emissions. Sander says, "At the start of July 2020, we presented SHS with five certificates confirming CO₂ emission reductions. By using our services, the company generated 80,000 tonnes less carbon dioxide in 2019. It also meant 4,000 fewer inland waterway trips and some 200,000 fewer lorry runs, which reduced congestion on the motorway." A smaller carbon footprint is a significant factor in SHS's move towards greater sustainability, which is why the certificates' presentation was marked by an event which saw Pierre Timmermans, DB Cargo's Board member for Sales, hand the documents to Sybille Ehlers-Morais de Oliveira, managing director of SHS Logistics. Timmermans also views the strategic partnership between SHS and DB Cargo as a success: "We are supporting this transition at SHS in our capacity as the company's environmentally friendly and efficient logistics partner. Our network offers the company an environmental benefit in addition to logistical advantages. We want to continue with our successful joint mission of shifting more freight to the rails."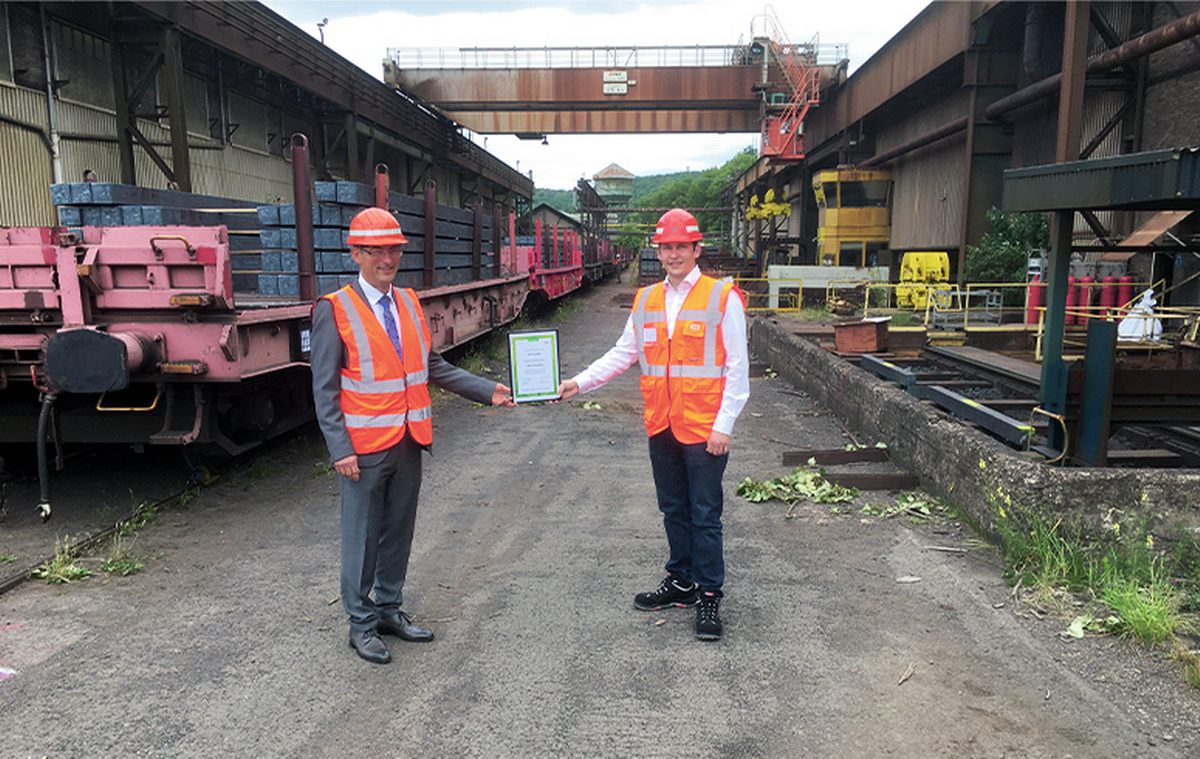
Left to right: Mike Schmidt, Saar-Rail, and Stephan Denzer, DB Cargo, with the CO₂ reduction certificate. Copyright: Michael Neuhaus
Looking at transports throughout the value chain
Cooperation between SHS and its rail service provider also goes beyond the company's immediate brief. As Sander explains it, "When transporting freight, we apply the principle of 'total optimisation'. This means that we study transports along the entire value-added chain at SHS and adjust them accordingly to ensure they are efficient." This has a number of implications. One is DB Cargo's close coordination with Saarstahl's rail company Saar-Rail when providing services such as shuttle train transports. This in turn enables both sides to develop highly efficient deployment plans for staff, wagons and locomotives. Looking ahead to the future and the digitalisation of logistics, SHS and DB Cargo plan to continue expanding their digital information-sharing activities. "Currently, we are jointly developing a range of solutions which will increase transparency and make for improved planning," Grossman says. For example, the business partners intend to digitalise the procedures for maintaining supplies of empty wagons, which will improve performance when dispatching rolling stock and optimise plant logistics processes. Innovative freight wagons are another item on the agenda. SHS and DB Cargo are working together to develop new types of freight wagons so they can increase transport efficiency even more. The goal of both companies is to have modular, weight-optimised freight wagons at their disposal. "The special thing about our partnership is that we have put so many of our collectively generated ideas into action," says Sander.